Collaborative group effort
Before sharing a specific case, let’s touch on Toyota’s Group Collaborative Activities.
Through this initiative, Toyota works with Tier 1 suppliers to solve problems faced by Tier 2 companies. It was born out of sessions set up in 2015 to share information and ideas between Toyota and the Group’s primary suppliers. Although initially the activities mainly consisted of Toyota providing information, from 2018 they also began to focus on mutual improvement and enhancing procurement in response to environmental changes affecting the auto industry. As part of these efforts, Toyota set out to strengthen the foundations of Tier 2.
Whereas the Smart Standard Activity (SSA) we introduced last time seeks to reduce costs by optimizing quality and performance standards, Group Collaborative Activities are aimed at improving Tier 2 productivity and work environments.
First, Tier 2 suppliers share their challenges. Then, the companies pursue improvements by incorporating TPS at the genba, receiving assistance from Toyota’s Global Production Center (GPC) and other non-procurement divisions as needed.
The initiative started in 2019, with 21 Tier 2 companies taking part as of October 2024. Among them is Umemura Industry Co., Ltd., the subject of this article.
Karakuri cart makes for safer handling
Based in Toyota City, Aichi, Umemura Industry supplies Hayashi Telempu, a vehicle interior systems supplier whose role is to develop interior trim packages by bringing together parts delivered by Tier 2. From Toyota’s perspective, Umemura resides in that second tier. Its core product is floor carpets. Of the company’s three domestic plants, the Fujioka Plant (Toyota City, Aichi) recently took part in the Group Collaborative Activities.
The Fujioka Plant manufactures carpets through the following process:
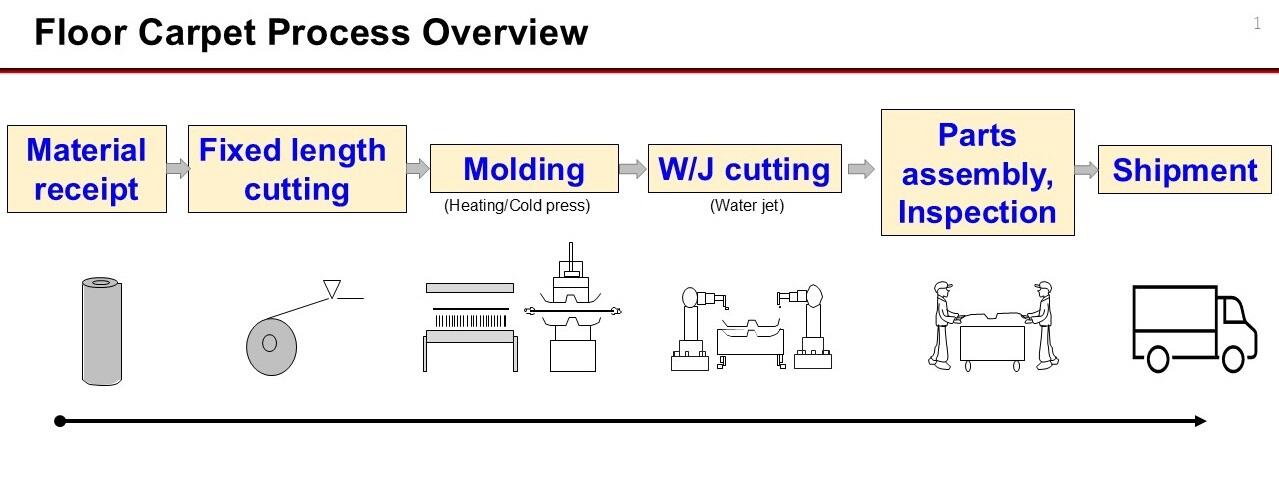
Although floor carpets are shaped differently for every car, when the material first arrives, it comes in uniform rolls.
The material rolls vary from model to model, with the heaviest rolls weighing some 90 kilograms. Before the collaborative improvements, these were taken from delivery trucks and laid flat onto pallets for transport into the plant. Once inside, each roll was then hoisted back upright, loaded onto a cart, and transferred to a storage area with lanes sorted by type.
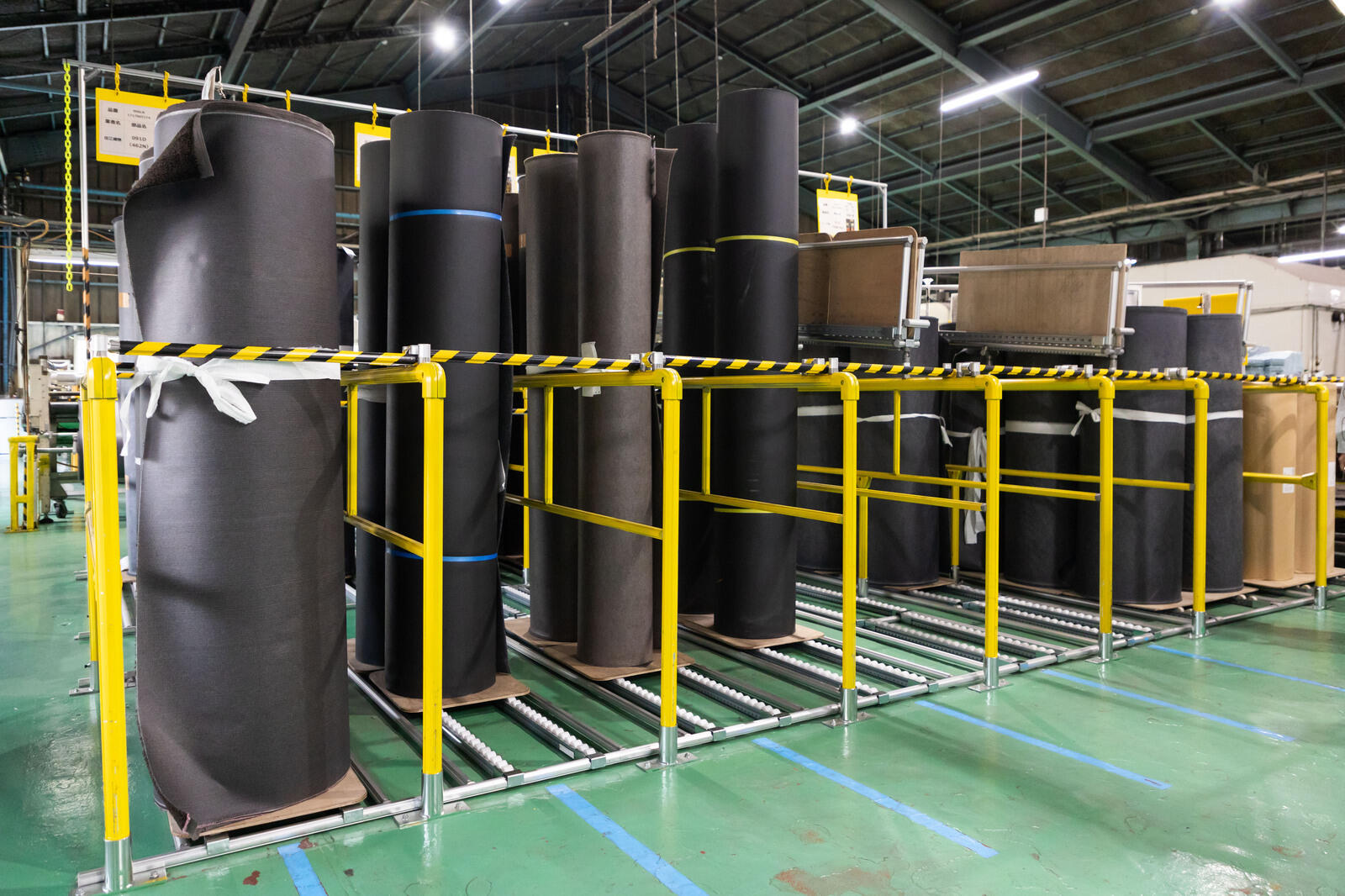
Lifting the rolls upright is physically taxing for employees while climbing on the stacked rolls carries its own risks.
The collaborative activities led Umemura to do away with the practice of laying rolls down flat when they are received and instead keep them upright from truck to pallet. The idea had never come up before—partly because Umemura had no pallets capable of transporting rolls in a standing position—until Toyota and Hayashi Telempu’s involvement spurred the improvement.
Gaining such outside perspectives is one benefit of the Group Collaborative Activities.
The video below shows how the task was performed before and after improvement, giving a good idea of how tough it was for workers.
The cart that appears in the “after” section of this video was built with help from GPC technicians. Instead of sensors and control devices, it uses a karakuri* mechanism that combines gears and shafts.
*Tools and mechanisms that use gravity, levers, and other mechanical solutions to boost efficiency or make tasks easier without the need for electricity or high-powered motors. Familiar examples include pedal-operated bin lids and self-opening umbrellas. In addition to curbing costs, karakuri also saves energy.
Unlike conventional carts, the new version is fitted with bars to prevent the roll from tipping forward, allowing it to be safely moved into a storage lane.
Another karakuri also helps transfer the rolls into the lane. Previously, this involved setting a base plate onto the lane, pushing the loaded cart onto the plate, and then pulling it out to offload the roll, which had to be supported by hand to stop it from falling over.
With the new cart, a base plate is set under the roll when transferring it from the pallet, so the cart doesn’t need to be pulled free. As the video below shows, a built-in bar is also used to slide the roll of material onto the lane.
Umemura’s workers note that they no longer have to worry about the rolls or themselves falling over, making the task easier.
Once the rolls are safely delivered, similar karakuri-based improvements can also be found in the cutting process.
Good ideas cost nothing
The next step involves drawing out the necessary lengths of material and cutting the roll into sheets. In the past, the entire roll would be cut up at once.
This was done to avoid returning the remaining roll to the storage area, which would involve getting it back upright. The result was a surplus inventory of cut sheets that required a large storage space.
Through the collaborative effort, Umemura shifted to cutting only the necessary pieces. Besides reducing the storage space by some 36%, this spares employees the extra work of cutting up an entire roll of material, making it easier to deal with sudden changes.
As for the additional task of righting the roll after cutting, to solve this problem, the team built another bespoke cart. By applying the principles of leverage, workers can now lift a roll of material with about a quarter of the force required to heave one up from the floor.